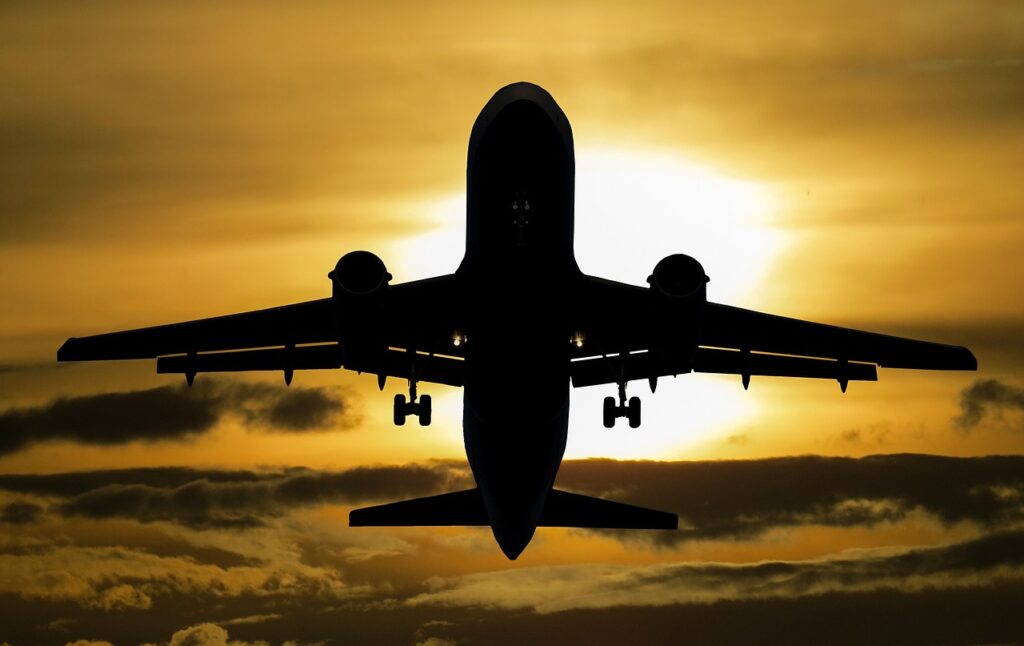
Industrial automation has significantly transformed the landscape of manufacturing across various sectors, with the aerospace industry standing out as a prime example of this technological evolution. Airplane manufacturing, known for its high stakes and stringent quality requirements, has embraced automation to enhance precision, efficiency, and safety. Among the various technologies propelling these advancements, servo drives and controllers have become indispensable tools, driving the precise movements required in the production of aircraft components.
Introduction to Automation in Airplane Manufacturing
Airplane manufacturing involves multiple complex processes, from the initial design and material selection to final assembly and testing. Each stage demands the highest levels of accuracy and reliability to ensure the safety and performance of the aircraft. As such, the aerospace industry has increasingly turned to industrial automation to meet these rigorous standards.
1. Precision and Quality Control: The primary advantage of automation in airplane manufacturing is the unparalleled precision it offers. Automated systems execute repetitive and intricate tasks with exact precision, which is crucial for maintaining the integrity of critical aircraft components.
2. Efficiency and Scalability: Automation accelerates production timelines and enhances the scalability of manufacturing processes. This is vital in an industry where the demand for new aircraft can fluctuate significantly based on various economic factors.
3. Cost-Effectiveness: While the initial investment in automated systems can be high, the long-term savings in labor costs, reduced waste, and increased throughput make automation a cost-effective solution for airplane manufacturers.
The Role of Servo Drives and Controllers
Servo controllers such as dkc11.3-200-7-fw are at the heart of many automated systems used in airplane manufacturing. These devices regulate the speed, position, and torque of motors that operate various pieces of manufacturing equipment, ensuring that operations are carried out with exact precision.
1. Assembly Lines: In the assembly of airplanes, multiple large and small components must be precisely aligned and assembled. Servo drives and controllers manage the motors that power automated assembly lines, ensuring components are manipulated and positioned with exact accuracy. This precision is crucial for assembling the fuselage, attaching wings, and installing windows and doors.
2. Drilling and Riveting Operations: Airplanes require thousands of rivets and fasteners. Servo-controlled drilling and riveting machines automate these tasks, performing them with high speed and accuracy. The precise control offered by servo systems ensures that every rivet is placed correctly, which is essential for the structural integrity of the aircraft.
3. Painting and Coating: The painting and coating processes of airplane parts also benefit from automation. Servo-controlled sprayers apply uniform coats of paint and protective coatings, crucial for both the aesthetics and longevity of the aircraft.
4. Inspection and Quality Assurance: Automated inspection systems, driven by servo controls, play a critical role in the quality assurance stages of airplane manufacturing. These systems use cameras and sensors to meticulously inspect each component and assembly for defects or misalignments, ensuring that every part meets strict aerospace standards.
Integration of Advanced Technologies
The integration of other advanced technologies has further enhanced the effectiveness of automation in airplane manufacturing:
1. Robotics: Robotics are widely used in various stages of airplane production. These robots, often equipped with servo systems, perform tasks such as lifting heavy components, welding, and assembling parts with precision that human workers cannot match.
2. Additive Manufacturing: 3D printing or additive manufacturing is becoming increasingly prevalent in the production of complex aircraft components. This technology allows for the creation of parts that are lighter and stronger than those made through traditional manufacturing methods.
3. Artificial Intelligence (AI): AI enhances automated systems by enabling them to learn from data and improve over time. In airplane manufacturing, AI algorithms analyze data from manufacturing processes to predict and prevent potential faults before they occur.
Challenges and Future Prospects
Despite the clear benefits, the integration of industrial automation in airplane manufacturing presents several challenges:
1. High Initial Costs: The cost of implementing sophisticated automated systems and training staff to operate them can be prohibitive, especially for smaller manufacturers.
2. Technical Complexity: The complexity of automated systems requires highly skilled engineers and technicians for operation and maintenance, posing challenges in workforce training and development.
3. Cybersecurity Risks: As manufacturing systems become more interconnected, they become more vulnerable to cybersecurity threats, which can have severe implications in an industry where safety is paramount.
Looking forward, the future of airplane manufacturing is set to be increasingly dominated by automation. As technologies evolve, the integration of more sophisticated AI, enhanced robotics, and advanced materials will likely make manufacturing processes even more efficient, precise, and cost-effective. The continued innovation in servo technology and controller systems will further refine these processes, ensuring that the aerospace industry can meet future demands with increased agility and reduced overheads.
Conclusion
Industrial automation, particularly through the use of servo drives and controllers, has profoundly impacted airplane manufacturing, setting new standards for precision, efficiency, and safety. As the industry continues to evolve, these technologies will play an even greater role in shaping the future of aerospace manufacturing, driving innovations that enhance the functionality and performance of aircraft while ensuring the highest levels of safety and quality.