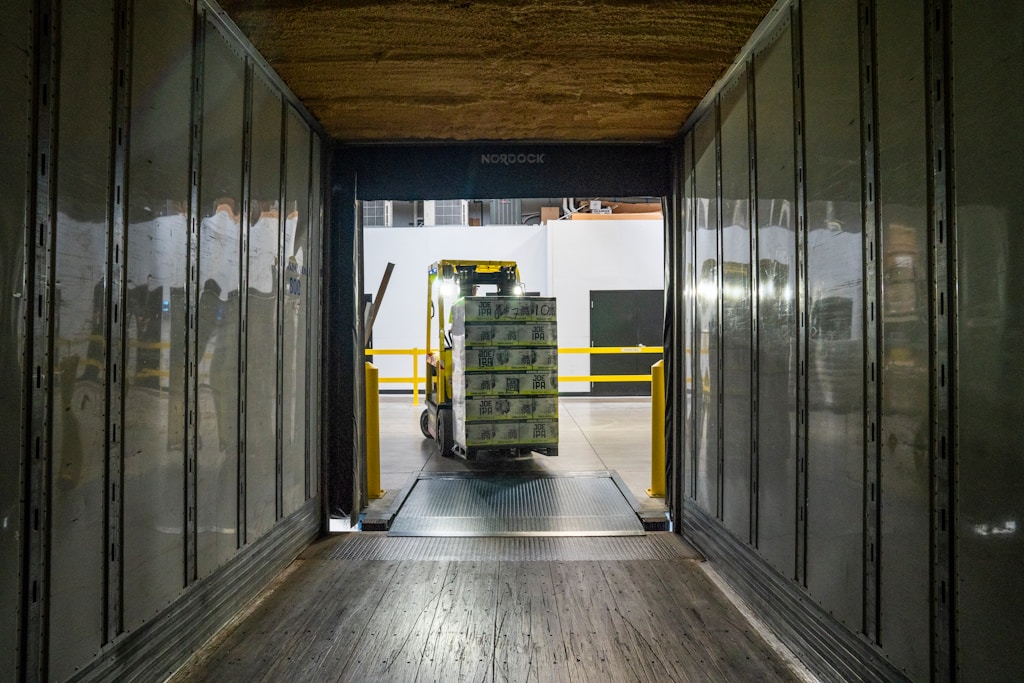
The process of manufacturing and delivering products into the hands of the customer is not just a mechanical connection of individual components but a well-thought-out network of activities called the supply chain. Let’s take a look behind the scenes of the supply chain, where each part plays a crucial role in the journey from raw materials to the final customer. Discover how it works, what supply chain management is for, and why proper management of this process is essential for the success of companies in today’s competitive environment.
What is a Supply Chain?
A supply chain is a network of individuals and companies involved in creating a product and delivering it to the consumer. The links in the chain begin with raw material manufacturers and end when the finished product is delivered to the end user.
The supply chain starts to function as soon as a company receives an order from a customer. Its basic functions include:
- Product development,
- Marketing,
- Operations,
- Distribution,
- Finance,
- and Customer Service.
What Components Does the Supply Chain Include?
The components of the supply chain include:
- Manufacturers,
- Warehouses,
- Distribution centers,
- Transportation Companies,
- and Retailers.
What Types of Supply Chain Models Exist?
There are several different supply chain models on the market. The selection of a specific model depends on the company’s structure and its specific needs.
Here are a few examples:
- The continuous flow model – is ideal for companies that manufacture the same products with minimal variations. Such products should be highly demanded and require minimal or no changes. This lack of fluctuation allows for streamlining production times and maintaining control over inventory.
- The fast fashion model – is ideal for companies that sell products based on the latest trends. Businesses implementing this model must get their products to market quickly to capitalize on prevailing trends. An example of an industry is fast fashion.
- The flexible model – is suitable for companies that produce seasonal or holiday goods and experience demand surges only at certain times of the year. The flexible model ensures their ability to quickly prepare for the start of production and efficiently end it in case of reduced demand.
What is the Purpose of Supply Chain Management?
Supply chain management is a key process – if optimized correctly, it can result in lower costs and shortened production cycles. Companies strive to improve their supply chains to not only reduce costs but also remain competitive.
Effective supply chain management can lead to reduced overall company costs and increased profitability. If one component fails, it is highly likely to affect the rest of the chain. Effective supply chain systems deliver each product piece at the right time to where it is needed. This is called the flow of production costs.
What is Cost Flow Management?
Efficient supply chain systems ensure that each product is delivered to the right place at the right time. Cost flow management most commonly applies to businesses that manufacture products with a large number of components from several different suppliers.
For example, a clothing manufacturer needs deliveries of fabrics, threads, and zippers to arrive at the same time. If some components arrive too early, they are stored at an additional cost. Conversely, delayed deliveries can lead to idle machines.
What Does a Supply Chain Manager Do?
The supply chain manager is responsible for managing and coordinating all activities within the supply chain. Their main goal is to optimize the flow of materials, information, and finances across the entire delivery process. Their tasks may vary depending on the needs and size of the company, but typically include:
- Planning and managing manufacturing and delivery operations,
- Managing storage and distribution,
- Responsibility for procurement, shipping, storage, and transportation activities,
- Monitoring and optimizing the performance of the supply chain,
- Managing risks and crisis planning in the supply chain,
- Monitoring and analyzing current trends in the trade sector,
- Evaluating customer needs, service offerings, and supply chain activities.
Overall, the supply chain manager seeks to ensure the most efficient and smooth operation of the supply chain, allowing the company to achieve its business goals and maintain its competitive advantage.
What Does Supply Chain Finance Mean?
Supply chain finance is an agreement in which the buyer collaborates with a financial institution that pays the suppliers on behalf of the buyer. These suppliers may opt into the program, but the responsibility for its establishment lies with the purchasing company.