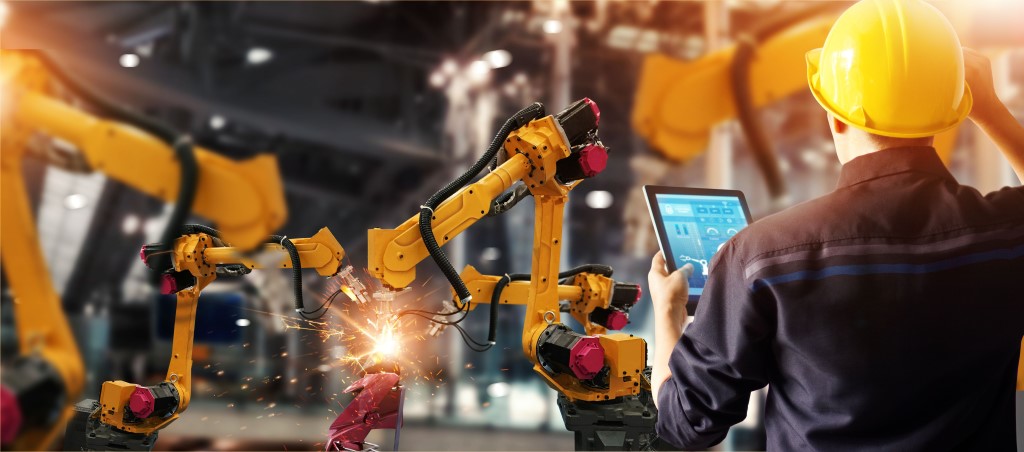
Introduction
In the dynamic landscape of the manufacturing industry, staying competitive and efficient is paramount. The integration of advanced software solutions has become a cornerstone for success, transforming traditional manufacturing processes into streamlined, data-driven operations. In this in-depth guide, we will explore the diverse array of software applications tailored for the manufacturing sector, examining how they enhance productivity, improve decision-making, and contribute to the overall success of businesses.
I. The Evolution of Software in Manufacturing
A. Historical Perspective
The manufacturing industry has undergone a significant evolution, from manual processes to automated systems. The advent of computers in the latter half of the 20th century marked the beginning of a digital transformation, paving the way for the integration of manufacturing software solutions to streamline operations.
B. Industry 4.0 and Smart Manufacturing
The fourth industrial revolution, often referred to as Industry 4.0, has ushered in an era of smart manufacturing. This paradigm shift involves the extensive use of digital technologies, automation, and data exchange to create a more interconnected and intelligent manufacturing environment.
II. Key Software Solutions in Manufacturing
A. Enterprise Resource Planning (ERP) Systems
Overview of ERP in Manufacturing
ERP systems play a pivotal role in integrating and managing core business processes, including production planning, inventory management, and order processing. In the manufacturing context, ERP software provides a centralized platform for real-time data visibility and decision-making.Benefits of ERP in Manufacturing
a. Improved Production Planning: ERP systems enable manufacturers to optimize production schedules, allocate resources efficiently, and reduce lead times.
b. Enhanced Inventory Management: Accurate and real-time tracking of inventory levels helps prevent stockouts, reduce carrying costs, and streamline supply chain operations.
c. Seamless Communication: ERP fosters better communication and collaboration across different departments, ensuring that everyone is on the same page regarding production goals and timelines.
B. Computer-Aided Design (CAD) and Computer-Aided Manufacturing (CAM)
CAD Software
CAD software facilitates the creation, modification, and optimization of product designs. It allows engineers and designers to create detailed 2D and 3D models, fostering innovation and precision in the product development phase.CAM Software
CAM software takes the digital designs created in CAD and translates them into machine-readable instructions for manufacturing equipment. This integration ensures accuracy and efficiency in the production process.
C. Manufacturing Execution Systems (MES)
Functionality of MES
MES acts as a bridge between ERP and the shop floor, providing real-time monitoring and control of manufacturing operations. It includes modules for production scheduling, quality management, and performance analysis.Advantages of MES
a. Real-Time Visibility: MES provides real-time insights into production processes, allowing for quick decision-making and issue resolution.
b. Quality Assurance: MES helps in maintaining product quality by monitoring and controlling various parameters throughout the production lifecycle.
c. Resource Optimization: By optimizing resource utilization, MES contributes to increased efficiency and reduced production costs.
D. Product Lifecycle Management (PLM)
PLM in Manufacturing
PLM software manages the entire lifecycle of a product, from conceptualization and design to manufacturing, maintenance, and disposal. It ensures that all stakeholders collaborate seamlessly across the product’s lifecycle.Benefits of PLM
a. Collaboration and Communication: PLM facilitates collaboration among cross-functional teams, ensuring that everyone involved in the product development process is on the same page.
b. Version Control: PLM systems maintain version control of designs and documents, preventing errors and discrepancies in the manufacturing process.
c. Compliance and Regulation: PLM helps manufacturers adhere to industry regulations and standards, ensuring that products meet the required quality and safety criteria.
III. Emerging Trends in Manufacturing Software
A. Internet of Things (IoT) Integration
The integration of IoT devices in manufacturing processes allows for the collection of real-time data from machines and equipment. This data is then analyzed to optimize production, reduce downtime, and enhance overall efficiency.
B. Artificial Intelligence (AI) and Machine Learning (ML)
AI and ML are increasingly being applied in manufacturing to predict maintenance needs, optimize production schedules, and improve quality control. These technologies contribute to smarter decision-making and automation.
C. Augmented Reality (AR) and Virtual Reality (VR)
AR and VR technologies are being leveraged for training, maintenance, and design validation in manufacturing. They enhance collaboration and provide immersive experiences for training and troubleshooting.
IV. Considerations for Implementing Manufacturing Software
A. Scalability
Choosing software that can scale with the growth of the manufacturing business is crucial. Scalable solutions ensure that the software can adapt to increased production volumes and evolving business needs.
B. Integration Capabilities
For maximum efficiency, it’s essential to select software solutions that can seamlessly integrate with existing systems. ERP, MES, CAD, and other software should work together to create a cohesive and interconnected manufacturing ecosystem.
C. User Training and Support
Investing in user training is vital to ensure that the workforce can effectively utilize the software. Additionally, robust customer support from software vendors is crucial for addressing issues promptly and minimizing downtime.
D. Security and Compliance
Manufacturing software often deals with sensitive data, including product designs and production schedules. Security measures must be in place to protect against data breaches, and the software should comply with industry regulations and standards.
V. Case Studies: Successful Implementation Stories
A. XYZ Corporation: Optimizing Production with ERP
XYZ Corporation, a leading manufacturer, implemented an ERP system to streamline its production processes. The ERP solution provided real-time insights into inventory levels, production schedules, and order fulfillment. As a result, XYZ Corporation experienced a significant reduction in lead times, improved resource utilization, and increased customer satisfaction.
B. ABC Manufacturing: Enhancing Quality Control with MES
ABC Manufacturing integrated MES into its production facilities to enhance quality control. The MES system enabled real-time monitoring of production parameters, leading to early detection and resolution of quality issues. This resulted in a substantial reduction in defects, improved product quality, and increased competitiveness in the market.
VI. Future Outlook and Conclusion
As the manufacturing industry continues to evolve, the role of software solutions will become even more integral. The ongoing integration of advanced technologies, such as IoT, AI, and AR, will further enhance efficiency and drive innovation in manufacturing processes. As businesses embrace these technological advancements, they position themselves for success in an increasingly competitive global market. The journey towards a digitized and interconnected manufacturing landscape is an exciting one, promising continued advancements that will shape the future of the industry. In conclusion, the adoption of software solutions in manufacturing is not just a trend; it’s a strategic imperative for businesses aiming to thrive in the digital age.
FAQ
What is the significance of software in the manufacturing industry?
Software in the manufacturing industry plays a crucial role in optimizing processes, enhancing efficiency, ensuring quality control, and facilitating data-driven decision-making.
What types of software are commonly used in the manufacturing sector?
Commonly used software includes Enterprise Resource Planning (ERP) systems for resource management, Computer-Aided Design (CAD) software for product design, and Manufacturing Execution Systems (MES) for shop floor control.
How does Enterprise Resource Planning (ERP) benefit manufacturing companies?
ERP software integrates various business processes, including finance, human resources, and supply chain, providing a centralized platform for real-time data, streamlined operations, and improved collaboration.
What role does Computer-Aided Design (CAD) software play in manufacturing?
CAD software enables engineers and designers to create detailed and accurate 2D or 3D models of products, facilitating the design and prototyping phases of manufacturing.
How do Manufacturing Execution Systems (MES) enhance shop floor operations?
MES software helps monitor and control manufacturing operations on the shop floor, providing real-time data on production status, resource utilization, and quality control, leading to improved efficiency and reduced downtime.
What is Product Lifecycle Management (PLM) software, and how does it benefit manufacturers?
PLM software manages the entire lifecycle of a product, from conception and design to manufacturing and end-of-life. It enhances collaboration, reduces time-to-market, and ensures regulatory compliance.
How does Quality Management Software (QMS) contribute to product quality in manufacturing?
QMS software helps manufacturers maintain and improve product quality by managing quality processes, monitoring compliance, tracking defects, and ensuring adherence to industry standards.
Can Customer Relationship Management (CRM) software be beneficial for manufacturing companies?
Yes, CRM software helps manufacturers manage customer interactions, streamline sales processes, and gain insights into customer preferences, contributing to better customer relationships and increased sales.
What are the advantages of adopting Internet of Things (IoT) software in manufacturing?
IoT software in manufacturing connects physical devices to the internet, enabling real-time monitoring, predictive maintenance, and data-driven insights to optimize operations and improve overall efficiency.
How can manufacturers ensure the security of their software systems in an increasingly digital environment?
Manufacturers can ensure software security by implementing robust cybersecurity measures, regularly updating software, conducting vulnerability assessments, and training personnel on cybersecurity best practices. Additionally, adopting secure coding practices is essential.