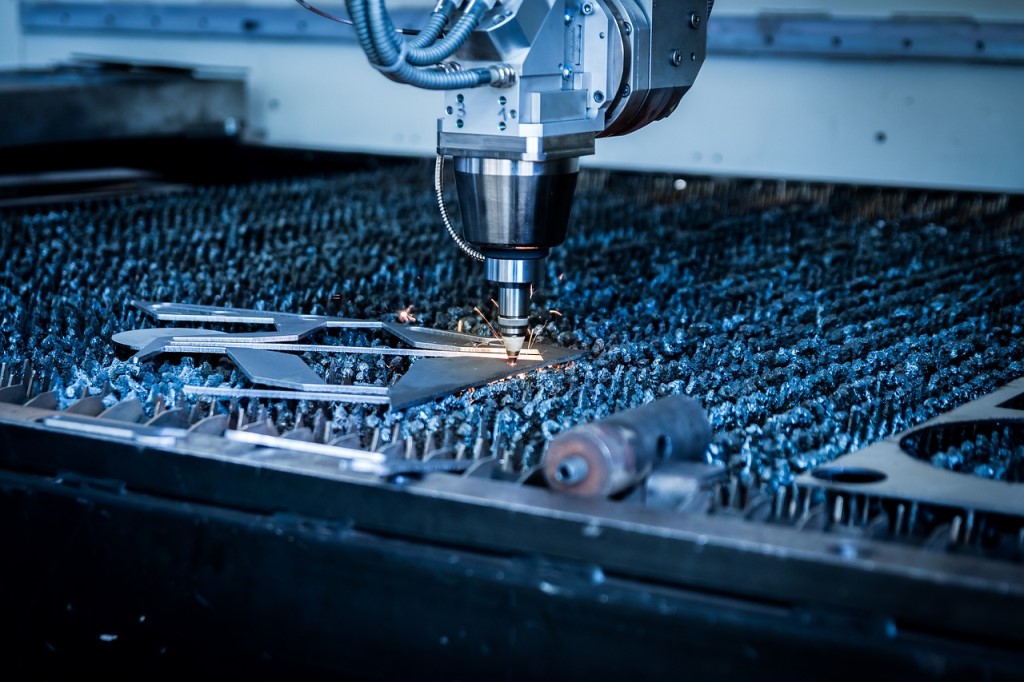
As we stand at the cusp of a technological revolution, we find ourselves increasingly surrounded by astounding innovations that reshape the landscape of various industries. One such marvel is Computer Numerical Control (CNC) machining technology, which has significantly revolutionized the manufacturing sector. Unleashing a new wave of potential, this article aims to delve into the exciting realm of CNC technology and provide insights into what its future holds.
What is CNC Machining Technology?
CNC Machining is an automated process used in the manufacturing sector that involves the use of computers to control machine tools. These tools can range from mills and grinders to lathes and routers. Essentially, CNC technology allows for precise control of design production through the use of a computerized interface, making it possible to produce complex shapes that would be almost impossible to achieve manually.
The Future Outlook for CNC Machining
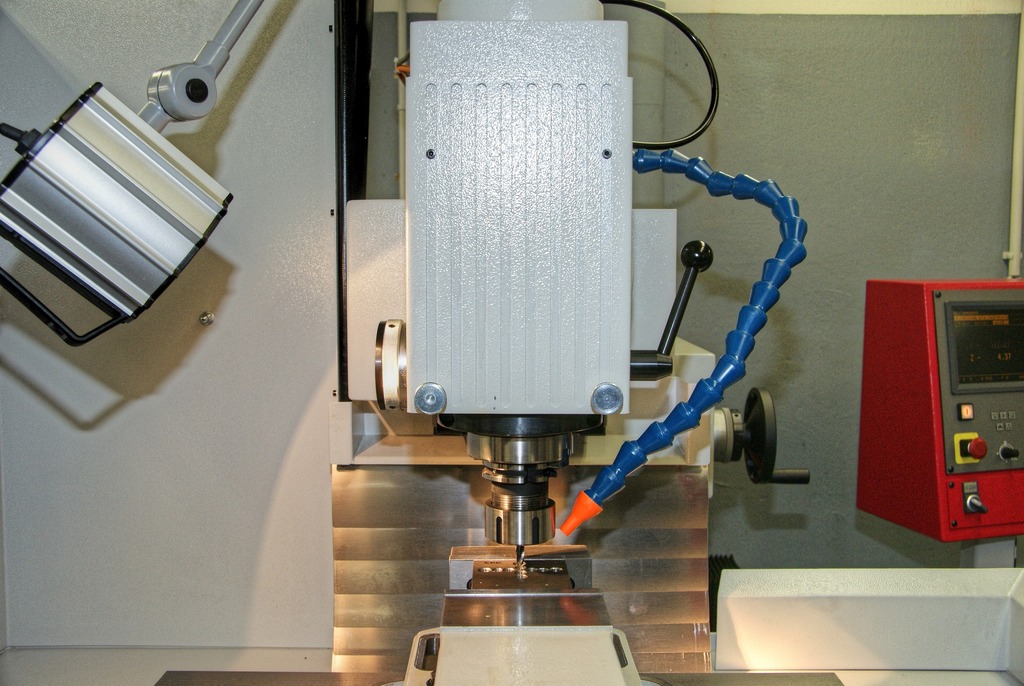
Peering into the future of CNC technology, we can anticipate a trajectory of continuous growth and evolution. This advancement will be spurred by key factors such as the integration of AI and machine learning, automation, and the rising prevalence of IoT.
Integration of AI and Machine Learning
Artificial Intelligence (AI) and Machine Learning (ML) are significantly influencing the future of CNC technology. With AI, CNC machines can operate with enhanced precision, optimize operations, and reduce waste.
AI-powered predictive maintenance can foresee potential issues before they occur, minimizing downtime and enhancing efficiency.
ML algorithms enable CNC machines to learn from previous operations, improving accuracy over time and refining the manufacturing process.
Increased Automation
The future of CNC machining lies in an increased level of automation. Advanced CNC machines are expected to have self-correction features, detecting errors and making adjustments in real-time.
The use of robotic arms in CNC machining is on the rise, enabling round-the-clock production and reducing labor costs.
Automated material handling and tool changing systems are likely to become standard features, improving production speed and efficiency.
Rise of the Internet of Things (IoT)
IoT is another critical factor shaping the future of CNC machining. By connecting CNC machines to the internet, manufacturers can monitor machine performance, optimize maintenance schedules, and improve overall efficiency.
IoT-enabled CNC machines can provide real-time updates about their operational status, enabling rapid response to any issues.
The integration of IoT can facilitate remote operation and monitoring of CNC machines, enhancing operational flexibility.
The Impact of Advancements in CNC Machining on Industries
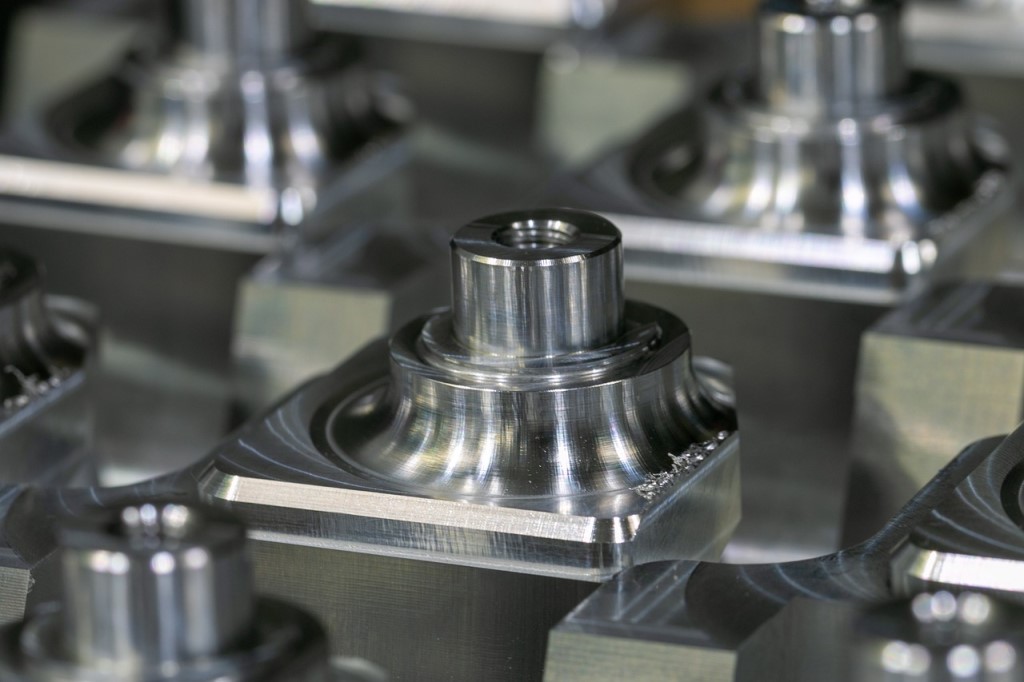
The future developments in CNC machining promise transformative changes across numerous industries. These advancements will redefine production standards, promote sustainability, and lead to cost savings.
Production Standards
As CNC machining becomes more advanced, we can expect a significant elevation in production standards. CNC machines of the future will be capable of producing CNC machining parts with complex geometries and intricate details that are currently beyond reach.
Promoting Sustainability
The improvements in CNC machining technology also have promising implications for environmental sustainability. By reducing waste and optimizing energy use, these advancements could substantially decrease the environmental impact of manufacturing operations.
Cost Savings
Investing in advanced CNC machines may initially seem costly, but these machines will eventually lead to significant savings. By increasing efficiency and reducing the need for manual labor, the total cost of production can be substantially lowered.
Preparing for the Future of CNC Machining
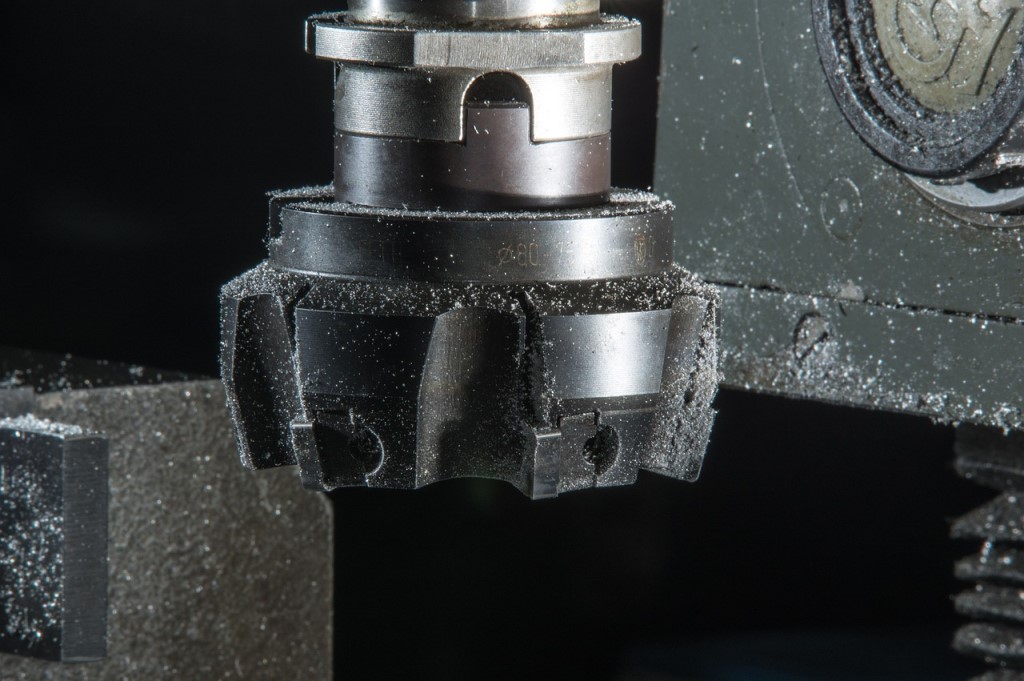
As we look forward to a future driven by technological advancements, it’s crucial for industries relying on machining with CNC to stay ahead of the curve. Below are some strategies they could consider.
Continuous Learning and Skill Development
With the ever-increasing sophistication of CNC machines, there’s a rising need for skilled operators who understand how to leverage these advanced tools. Workers need to stay abreast of the latest developments and continue to upskill.
Investing in professional development and training for existing workers.
Collaborating with technical institutions to create programs aimed at producing skilled CNC operators.
Investing in Advanced Machinery
To remain competitive, manufacturers should consider investing in the latest CNC machinery. Although these machines may come with a higher upfront cost, their efficiency and accuracy can lead to long-term savings.
Evaluating the cost-benefit ratio of investing in advanced CNC machines.
Budgeting for future technological upgrades.
Leveraging Data and Analytics
As the integration of IoT enables CNC machines to generate valuable operational data, businesses can use this information to drive improvements. Using data analytics tools, they can gain insights into machine performance, optimize maintenance schedules, and enhance overall productivity.
Implementing data analytics software to analyze machine data.
Using predictive analytics to anticipate machine failures and schedule maintenance.
Adopting a Proactive Maintenance Approach
Proactive maintenance can drastically reduce machine downtime and extend the lifespan of CNC machines. With predictive analytics and IoT, businesses can identify potential issues before they become significant problems.
Scheduling regular maintenance checks to ensure machine health.
Utilizing predictive analytics to foresee and address potential issues.
Conclusion
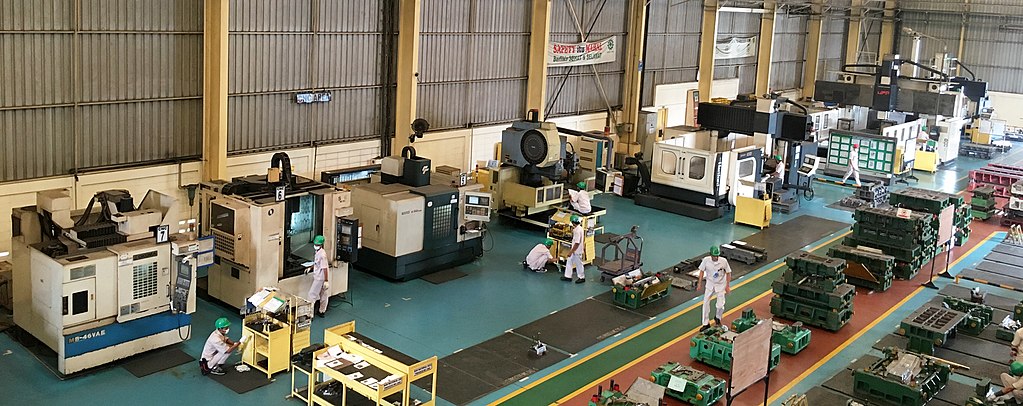
The future of CNC machining technology is teeming with potential and possibilities. With the integration of advanced technologies like AI, IoT, and automation, we’re poised to witness a seismic shift in the manufacturing landscape. The benefits extend beyond improving the efficiency and accuracy of manufacturing processes; they also herald an era of improved sustainability and reduced environmental impact.
However, this transformative potential isn’t without its challenges. Businesses and industries must prepare for these changes by investing in continuous learning, advanced machinery, data analytics, and proactive maintenance. By taking these steps, they can not only adapt to the future of CNC machining technology but also leverage its full potential to drive growth and success. In the final analysis, the future of CNC machining technology isn’t just about machines; it’s about people, strategies, and innovative mindsets embracing these advancements for a more efficient and sustainable future.