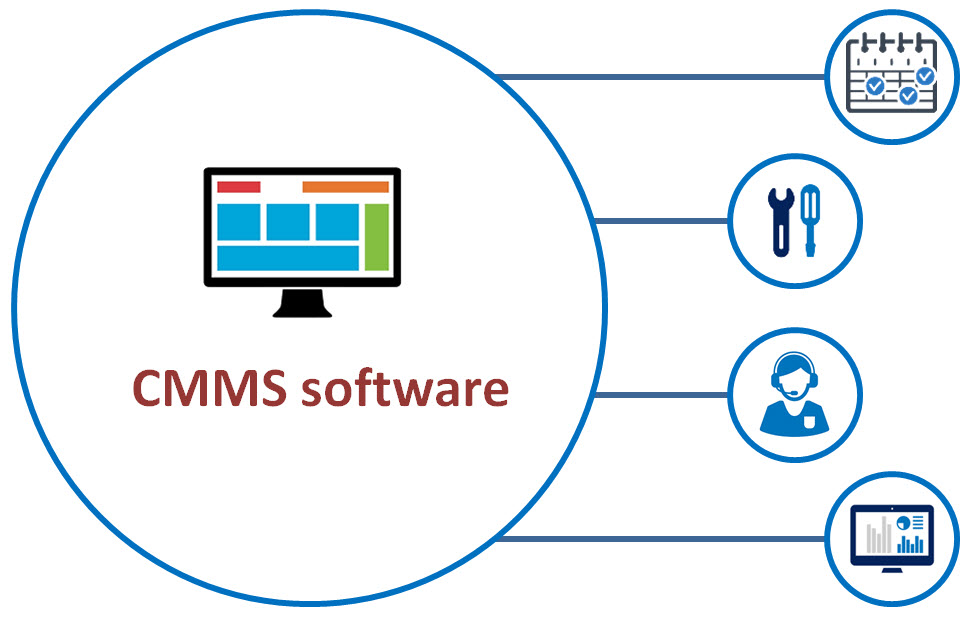
The high price of equipment essential to the production process and the increasing demand for top-quality products make it essential to maintain equipment capable of providing maximum availability of the equipment, high production quality, and safety throughout the entire production cycle. To achieve this, it is necessary to make use of technology capable of reducing the cost of maintenance, improving the availability of equipment, and improving the technical team security by intervening when needed when breakdowns or shutdowns occur.
Like software like the CMMS (Computerized Maintenance Management System) software, maintenance management systems guarantee the worldwide control of maintenance log and can be a great partner for any company in any industry.
CMMS software plays an essential function in combining preventive and corrective maintenance plans. It permits managers to keep track of the entire inventory of assets and equipment by setting up and implementing preventive or corrective maintenance plans. Despite the apparent benefits that preventive maintenance offers, there’s equipment that, by its nature, requires proper maintenance programs.
When using the CMMS solution like Limble CMMS which is one of the best CMMS software, it’s possible to manage all maintenance procedures by monitoring the actions performed in real-time and analysing the material consumed, services rendered and the associated expenses. The information recorded will be incorporated into each asset’s historical record, allowing you to assess its performance quickly, the frequency of repairs needed and associated costs, the duration of service, and the impact on the company’s profitability. Additionally, all of this data is available in real-time.
The Benefits of CMMS in Maintenance Management
A CMMS provides various benefits not available in spreadsheets, or other manual methods of tracking maintenance. The central nature of a CMMS, as well as the automated features it offers, yield efficiency in record-keeping, scheduling, and data management, as well as overall efficiency. They include:
Organized Maintenance Scheduling
When maintenance must be executed on sizeable mechanical equipment or tenant pipes or tenant piping, the CMMS helps a facility make maintenance scheduling easier. Specific CMMS software allows the fine-tuning of schedules for any maintenance an organization employs and supports a wide variety of schedules.
Scheduling is most efficient in organizations that employ various maintenance methods within the same space. A CMMS helps managers to have an overview of their strategies for maintenance- reactive or proactive maintenance, for instance. It also lets them look into specific strategies to assess how tasks are completed.
Simplified Record-Keeping
Suppose you’re using a CMMS to manage inventory. In that case, it will allow you to quickly track the expense of spare parts utilized for the maintenance and create reports to analyse the information further. This will optimize the order of parts and utilization. Maintenance and repair tracking using CMMS helps simplify keeping records to ensure compliance audits are kept in order and keeping these essential items in one easily accessible location.
More Safety and Less Risk
A damaged or malfunctioning equipment can be dangerous, posing a greater risk to the safety of employees and the operators. A cmms computerized maintenance management system can reduce risks and improve the safety of operators by ensuring that equipment functions within acceptable limits and all safety elements and features are functional. Furthermore, CMMS software facilitates work permit management and safety procedures, risk management administration, legislative compliance, and much more.
Real-Time Information About Assets
Without the CMMS, it’s impossible to gain any perspective from a bird’s eye view of the assets in a facility. A CMMS lets the user see a range of assets, typically using colour codes or symbols to represent various health levels of assets, so it’s much easier to comprehend the facility’s overall health in one glance.
This makes it simple to identify problems within the facility. By examining one particular area of a building concerning the rest, the maintenance manager will identify where their attention is required the most. For instance, in Limble CMMS, it is possible to filter work orders based on areas inside the facilities. The areas with the highest priority work tasks can be given priority over other areas when there’s an extensive backlog of maintenance work, and the labour resource is limited.
Predictive Maintenance Is Made More Accessible Through Data Collection
Since your CMMS is collecting data regarding repairs, maintenance, and inventory utilization, it will utilize the information to determine the timing of maintenance projects. Data-driven companies prefer this method to alert maintenance teams of imminent issues before they occur. This results in less unplanned downtime and more maintenance which addresses actual issues rather than merely following an established schedule, regardless of whether it’s necessary.
Audits Can Improve Safety by Ensuring Compliance with Audit Systems
The reality is that the facility manager is likely to have many things to be aware of daily. The goal of using a CMMS, in this case, is to simplify or automate the tasks that otherwise require continuous supervision and lengthy analysis of data.
It also reduces the number of items the maintenance team at a facility must remember. As time passes, the facility will become more efficient and reliable, allowing maintenance personnel to concentrate on urgent issues.
Work Orders and Request
Before the invention of CMMS, work orders required an immense volume of documentation, sorting, and physical file structure. CMMS software aims to create work orders more easily categorizable system that allows employees to send requests for work and managers to keep track of the work requests. Work orders are then given to the right team or technician to complete.
Based on the CMMS, work orders could even be generated automatically after certain conditions are fulfilled (cycle counts of the machine, work orders made by specific people, or even the readings of the sensor for monitoring conditions).
Reduce the Need for Paperwork
Using software to manage maintenance and facilities management will eliminate the requirement for clipboards and paperwork since the software can automatically record information. Maintenance personnel can also look up all the work orders on their computer and mobile gadgets. Thus, maintenance personnel aren’t required to look through file cabinets and folders to locate the information they require.
Increases the Knowledge of Maintenance Technicians
In a CMMS, it is possible to store user manuals in PDF by the asset. Mobile-based CMMS allows technicians to have access to the manuals from their location by providing step-by-step instructions and documentation for repairs. This significantly reduces human error. In addition, PM/PdM tracking makes the task and procedure documentation easy. The historical data about the failures is also easily accessible with a CMMS.
CMMS software image source: swefc.unm.edu