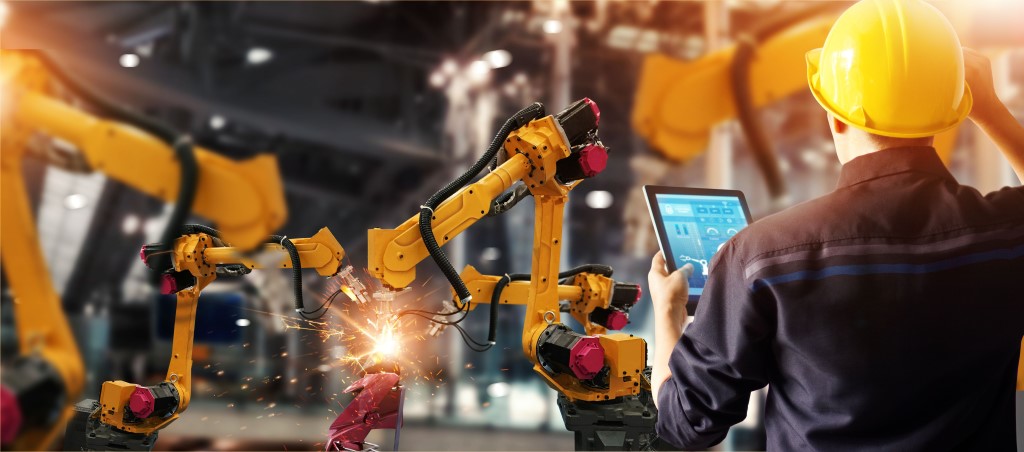
Manufacturing industries are being revolutionized by robots. In manufacturing and production settings, robots are designed to move materials and perform various programmed tasks.
Robots perform repetitive work that could lead to boredom, as well as other duties deemed unsuitable or dangerous to human workers due to the high tendency to cause injuries.
Here are the common uses of robotics in today’s manufacturing industries.
1. Materials Handling
Robotic material handling systems are very useful in material handling applications and other manufacturing applications. The robotic material handling systems are used in various applications, such as manufacturing, transportation, packaging, warehousing, maintenance, construction, and other heavy industries. The robotic material handling systems are mainly divided into two categories. The first category is known as machine loading, while the second category is referred to as unloading and transportation systems.
One example of a robotic material handling system is the palletizing system. A palletizing system is used to pack and load goods at a warehouse or distribution centers. Palletizing system has multiple functions, including automatic loading and unloading systems. The robotic material handling systems can be found in both industrial and non-industrial applications, and they’ve been a great help for the industries.
2. Cutting
In cutting machines, there are several types of robots available. Some of them are capable of cutting metal in a wide range of sizes, without damaging the core of the metal. There are also others that are capable of cutting metal in a very narrow size and, also, in a precise manner. These robots are used to cut heavy-duty pieces of steel, which are very hard to break. In fact, they’re mainly used for cutting large amounts of steel. Cutting robots are extremely reliable and perform their task very well.
3. Welding
A good welding robot is one that works by welding and, then, cutting or routing accordingly. A routing robot works on the same principle. These robots are generally used for different jobs, depending upon the application.
In welding, an end effector is generally attached to the robot, which does the actual work. The welding robot controls the heat of the welding rod, so that the welding process gets completed in a proper way.
There are different uses of industrial robots in the welding industry. A basic welding robot is, basically, a machine that’s capable of doing basic welding tasks, like cutting, heating, etc. There are different types of welding robots available in the market, and each type has its own unique characteristic. The main purpose of these welding robots is to perform these tasks in the most accurate manner, as well as to give correct output as per the specification.
4. Assembly
Other types of industrial robots are the ones that are used in assembly lines in factories. The main focus of these robots is the assembly of production materials, which is one of the most common applications of robotics in the manufacturing industries. These robots are now being used in the production of machines, such as food processors, vending machines, and even in construction sites.
These robots can do the job by manipulating the parts in a controlled manner, reducing the risks to the consumer, as well as the worker performing this task. In addition, assembly robots are also used in manufacturing plants. They help reduce labor costs and increase efficiency, allowing the company to make products faster.
5. Dispensing
The application of an automatic dispensing machine is quite similar to the use of robotic arms. There are various uses of industrial dispensing robots, and they have certain end effectors to do the task in hand. Industrial robots used for dispensing have two types. One of them is an automatic dispenser, which is the basic one that acts as a push-button dispenser. The next type is a robotic arm that has an electric motor attached to it. These robots perform tasks, such as spraying, applying adhesive, gluing, and painting with utmost accuracy.
6. Material Removal
The most common applications of industrial robotics are the ones that deal with material handling or material removal. This could be anything, from removing materials to come up with finish products for mining operations to processing plants, oil drilling, and construction. These systems do the actual work by manipulating the materials in a controlled manner, without risking human injury. That’s a very useful feature for many industries today because it means that there’s less risk of damage to human workers.
Conclusion
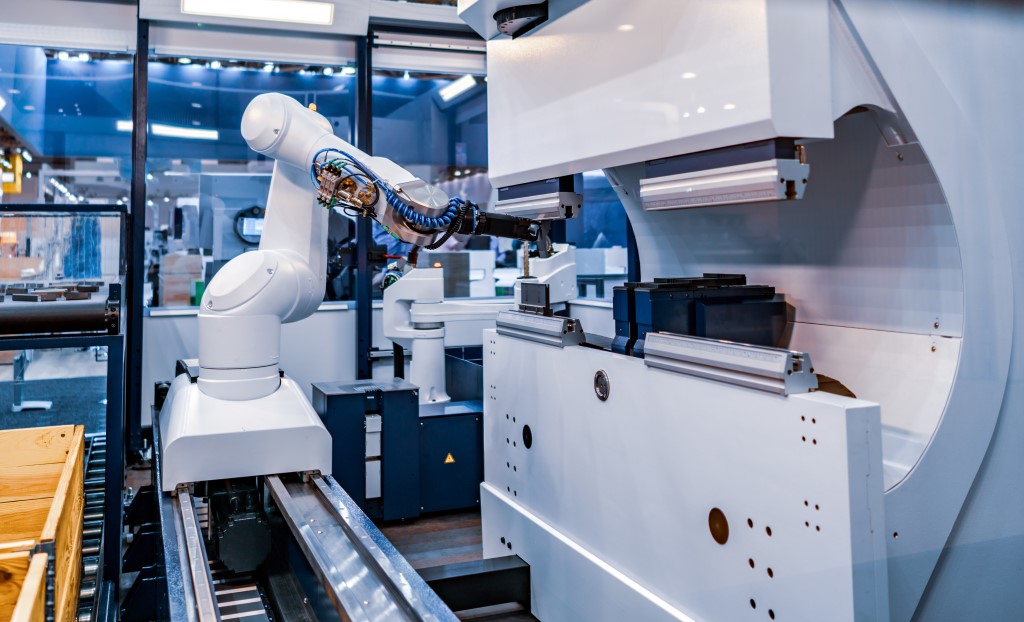
Every job is performed by robots with precision and super repeatability. The applications discussed above are a proof of their significance not only in manufacturing industries, but also in other sectors. No wonder why they’re considered to be one of the means for technology to change the world by 2025. Indeed, they can significantly improve product quality. Their reliability is second to none. Most importantly, industrial robots increase safety in the workplace.