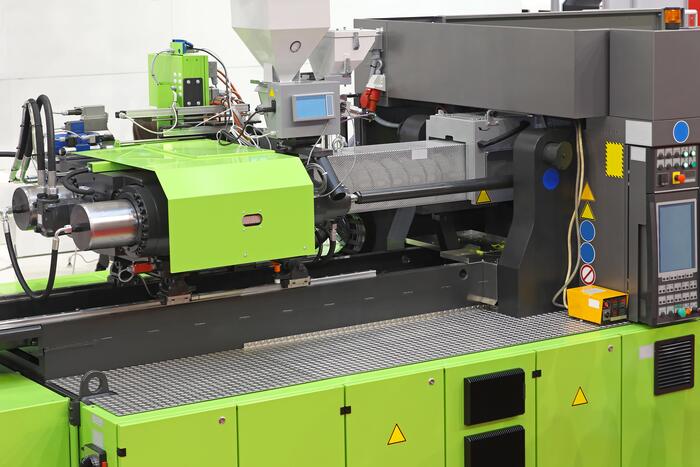
Increasing throughput on your injection molding process can be quite complex. If you choose to fill and cool molds too fast, you’re probably going to have a greater number of rejects. And when the process is to slow, you’re more likely to incur higher production costs. The key thing here is to maximize throughput. That’s why you need to carefully choose a proper chiller for your molding process.
As a business owner, you really want to make sure that you get the most out of your production process. To optimize productivity in an industrial process, you should pay close attention to your cooling system. Remember, injection molding is a delicate process that requires proper cooling. So, be sure to incorporate a high-quality chiller into your process.
Understanding the Injection Molding Process
Cooling is extremely important in molding cycles. This is because the part’s material should solidify in the mold before it is ejected. Without proper cooling times in your manufacturing process, there’ll likely be a greater number of defects like wrapping and distortion. This is mainly because the thermoplastics plus other materials that make up the part should be cooled properly for it to attain the desired structural integrity.
In injection molding, cooling takes the largest amount of time. And cutting the time too short might result in a significant number of product defects. To optimize throughput, the best thing to do is to find an acceptable cooling time for the component being created. So, be sure to install proper cooling to eliminate the necessary amount of heat.
Because of the high number of injections, the mold ends up accumulating excess heat. Working with process chiller experts who’ve extensive experience working with injection molding applications will make it easier for you to prevent this heat accumulation and achieve uniform cooling times.
In the molding process, there are two common points of heat transfer. One exists between the plastic and the mold while the other one is between the mold and the coolant. So, make sure that your process is designed properly at these points so as to minimize cooling time and deliver efficient cooling. Designing efficient mold channels is extremely important. The coolant should also be sufficiently cooled in order to prevent heat accumulation and remove excess heat from the cycle. A properly sized chiller will be able to provide enough heat removal and prevent excessive buildup of heat in the mold.
Why is Cooling Essential in Molding Cycles?
When it comes to injection molding, there are three stages involved; injection, mold cooling, and mold opening plus injection. Without proper cooling, there’ll be a greater number of part defects, including warping and distortion. This is mainly because the materials that make up the mold must be allowed to cool properly so as to ensure structural integrity. For companies in certain industries, such as medical plastic injection molding companies, ensuring product quality is not just a matter of legal compliance and reputation, but safety as these products may come into contact with vulnerable people or even be used in surgical procedures.
In injection molding, cooling consumes the largest amount of time. To maximize throughput, it’s therefore important to find an acceptable cooling time for specific products and ensure that you’ve proper cooling systems to remove the desired amount of heat.
Working with process chiller experts who have got the experience working with such applications makes it easier for you to prevent this heat accumulation and achieve uniform cooling times.
How to Minimize Cooling Time?
In the molding process, there are two common points of heat transfer. There’s one between the plastic and the mold itself and another between the mold and the coolant. With a properly designed process, you can minimize cooling time and deliver efficient cooling.
For maximum heat removal between the plastic and mold, incorporating efficient mold channels is extremely important. And for proper cooling between the mold and the coolant, it’s crucial that the coolant is sufficiently chilled to prevent heat accumulation and also remove the heat added during each cycle. At this point, chiller selection is critical. A good-sized chiller will provide adequate heat removal and prevent heat buildup in the mold.
What to Consider When Purchasing a Chiller?
Chillers are available in all sizes, from large, planet-sized units that deliver over 500 tons of cooling per hour to portable models that deliver a single ton of capacity per hour. Then, how do you choose the right one for your application needs?
You’ll need to start by calculating the tonnage or chilling capacity required to deliver the lowest water temperature to your process. That’s the total amount of heat that should be removed from the molded and extruded plastic.
Basically, there are two common ways to size a chiller. One of the simplest methods is the use of sizing guidelines, formulated by experts. These guidelines usually cover all heat-generating aspects of typical injection molding processes, including temperature controllers, material type, specific heat, cooling tanks, hydraulics, pumps, motors, barrel or mold heaters, as well as dryer-after coolers.
Starting with materials, determine the estimated heat loads for each attribute associated with your process, and then sum up the results to obtain the approximate tonnage of cooling capacity required.
Chiller Sizing
To correctly size an injection molding chiller, consider the constant cycle time. This is a very important element for maximizing system throughput. For you to deliver reliable cooling you should gather sufficient data about your process. Determine your heat removal requirements, flow rates as well as temperature drops.
If you’ve multiple molding machines, Variable and Load-Matching chillers will enable you to deliver ample cooling for all the units. As the heat load rises, the chiller will react accordingly to ensure that the right coolant temperature is maintained. This will, in turn, minimize downtime, increase production levels, and significantly improve your profits.
Conclusion
Injection molding has become so popular in today’s manufacturing world. But without proper cooling, this production technique might not be effective as you need it to be. Incorporating a chiller into your application’s cooling system will ensure that the right temperature is maintained all through. Plus, you’ll be able to get high-quality parts that are both durable and aesthetically appealing.