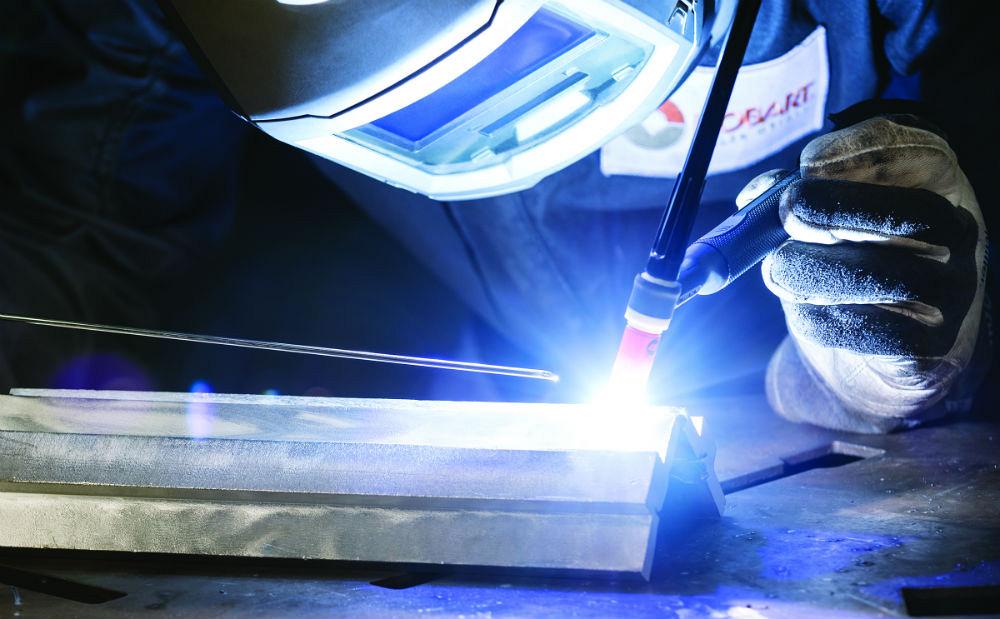
Welding is more than just a skill and happens to be a complicated process that involves several things such as different matters, heat, electricity, and oxidation. With so many things going on at the moment, there are chances of problems occurring that could lead to weld failure.
The choice of metal plays a key role in making your weld a success or a failure. Here are the top 4 metals for welding:
- Aluminum
- Low Carbon Mild Steel
- Stainless Steel
- Other Metals
1. Aluminum
Welding aluminum is trickier than low carbon steel, and it can be welded without much difficulty if you possess the proper technique and knowledge. The main thing to bear in mind is the right selection of grades. You don’t need much effort to weld grades in the 1XXX series. You need filler material in welding grades in the 6XXX. Aluminum in the 2XXX series is not easy to weld, but you can weld a few grades of this series, using the proper technique and filler material.
Another thing in welding aluminum is the strength and durability of the material. Some of the aluminum alloys like those with T6 designation are artificially aged to increase the strength. They are heated to a certain temperature for a particular amount of time. During the welding of these grades of aluminum, the intermetallic triggers change their form.
To make these aluminum alloys back to their original power, they have to be artificially aged a second time via a heat-treatment process.
2. Low Carbon Mild Steel
Low carbon mild steel is one of the most weldable metal. This is due to several different factors. One of the reasons behind excellent weldability its long history of being used in a variety of applications.
Low carbon steel can be welded as it is more ductile compared to others. This is due to the low amounts of carbon and trace amounts of other alloying elements. This keeps the formation of brittle microstructures away like martensite. This removes the risk of certain types of weld failures, such as hydrogen cracking.
3. Stainless Steel
Stainless steel is a metal you can easily weld with the proper technique and knowledge. Numerous stainless steels that are known for their corrosion resistance can be welded. You should know the grade of the stainless steel that is being welded. There are three major types of stainless steel:
- Austenitic
- Ferritic
- Martensitic
Several of ferritic stainless steels are extremely weldable and you can weld austenitic stainless steel too. But as for martensitic stainless steel, they are difficult to weld due to their hardness and propensity to crack.
An important thing to consider when you are welding stainless steel is intergranular corrosion. They can occur when the stainless steels are subjected to high-temperature environments such as welding. In that case, the chromium could join with the carbon present within the steel and this formation prevents chromium to mix with oxygen. As a result, there are no chances of chromium oxide layer being formed. The oxygen then combines with the iron present in stainless steel that leads to corrosion. There are some methods available that could prevent this such as using titanium or niobium such as Grade 321. Another way to prevent intergranular corrosion is via using low carbon stainless steel.
4. Other Metals
Though exceptions are always there, welding gets a bit difficult with other types of metals. Such as the welding of titanium would require extra equipment or shielding to keep it from oxidizing. Steels with a high amount of carbon require a post-weld and preheat heat treatment to prevent cracks from appearing.
You can weld some superalloys in a vacuum. You should individually research all the metals that you want to weld so that you can select the best welding methods. Speaking of the best welding method, you must invest in the best welding protective gear including a welding helmet. For stylish and durable welding helmets, visit Welding Corner.