Vacuum casting is a process that can provide a fast and a precise way to manufacture plastic parts at a small scale. The technique excels at pre-production parts, design verification, and low volume manufacturing.
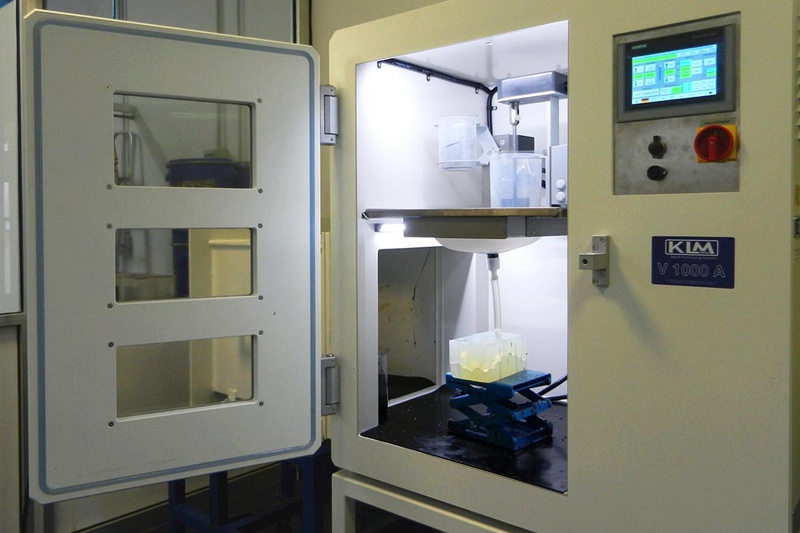
1. A Low-Cost Method for Making Small Batch Plastic Prototypes
The vacuum casting technology is a soft tooling based technique used to manufacture plastic parts. Modern developments have widened the range of plastics that can be cast into silicone molds. This offers a great opportunity when you need a small number of prototypes, pre-production samples or functional prototypes.
Polyurethane casting is similar to injection molding but for a few important features. First, the mold is made of soft silicone instead of steel as it is usually done in injection molding. Second, since the mold is created from liquid silicone, it requires a master pattern and this is usually manufactured from a metal bland using CNC machining or from a 3D-printed part. The main advantage of urethane molding is that it can achieve the same results as injection molding but there is no need to invest in expensive metal tooling.
Vacuum urethane casting is a bridge process between mass production and prototype manufacturing. It can also serve you for functional testing and pre-marketing batches. And if your industry relies on quick turnaround heavily, urethane casting can help you bring that next model to the market faster.
2. Making Master Patterns for Vacuum Casting
One of the most important things to ensure high-quality cast urethane parts is the precision of the master pattern. After all, it’s the master pattern that determines the cavity properties and what will be copied to each part of the batch. For example, if a small chip was made during the manufacturing of the master pattern, the same chip will appear in every part of the batch. That is why masters are machined to a +/-0.05mm tolerance and are often manually processed for a better surface finish in cases where a glossy texture is required.
In order to achieve optical clarity or obtain a glossy finish, a number of consecutive grinding and polishing operations is applied to the part. In some cases, where a specialized surface texture is necessary, the master pattern is painted in a way that provides this texture and as the mold is made, the texture of the master transitions to the texture of the cavity and, naturally, the manufactured part. The finishing operations are quite complex and require specialized experience and equipment, so polyurethane casting services and prototyping shops are often employed to manufacture the master pattern.
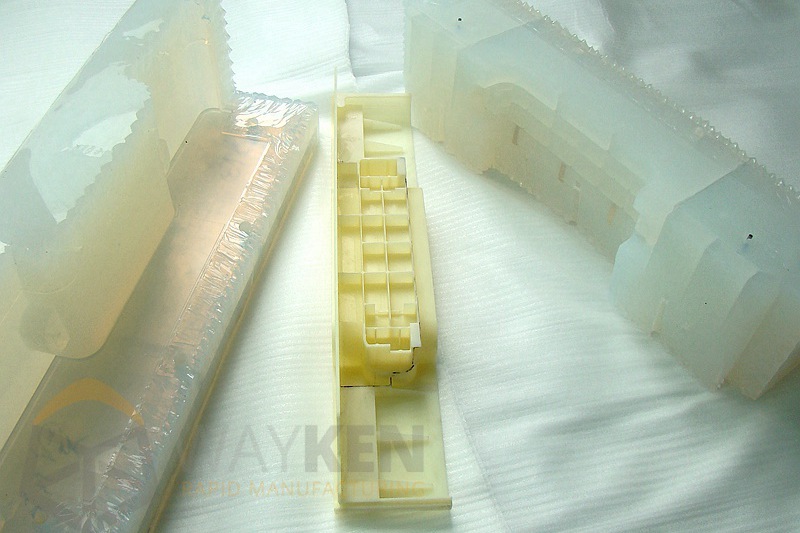
3. Silicone Rubber Mold Making
As was said earlier, the urethane casting mold is made using the master pattern. Silicone is very stable (does not react with other liquid materials or plastics), it doesn’t shrink and can flow into the most complex of crevices.
A silicone mold is an example of soft tooling. It is easily manufactured but its durability is not very good. Depending on the part, you can obtain from 20 to 10 parts before the mold becomes too damaged to provide the required precision of the end-part.
Steps to Creating a Silicone Rubber Mold:
- The master pattern is covered in a special film to ensure efficient removal from the mold.
- The master is suspended over a tank and additional mold elements are attached to it.
- Liquid silicone is poured over the master pattern and simultaneously, the air is sucked out of the tank to ensure that no bubbles remain inside the mold.
- The mold is cured in the oven at 40℃ for 8 up to 16 hours.
- The master pattern is removed from the mold as well as all the additional elements. The mold is ready.
4. Polyurethane Casting Process Detail
Urethane vacuum casting is great for its wide range of materials, colors, surface finish options and turnaround time. However, the durability of the molds is quite short, so their condition must be monitored closely. In order to achieve maximum repeatability the following factors must be controlled and taken into account: mixing, de-gassing, stirring, preheating, casting and de-molding. Such rigorous control requires specialized and expensive equipment, that is why some companies who need a considerable number of vacuum cast prototypes employ vacuum casting services. They usually have more experience and faster turnaround time. Not to mention, precision and repeatability. For example, some polyurethane vacuum casting services in China can provide a consistent tolerance of ± 0.15mm/100mm and a peak precision of ± 0.05 mm.
Steps to Urethane Casting Process:
- The mold is heated to 60-70°C in an oven.
- The mold is assembled and a release agent is applied to provide successful part removal.
- Polyurethane resin is heated up to 40°C. Two-component resins (colored or other) are stirred and degassed in a vacuum.
- The resin is poured into the cavity of the mold and is cured in the oven again. Usually, from 1 to 6 hours.
- The cast part is removed from the mold and all the additional elements are removed as well. The part is ready.
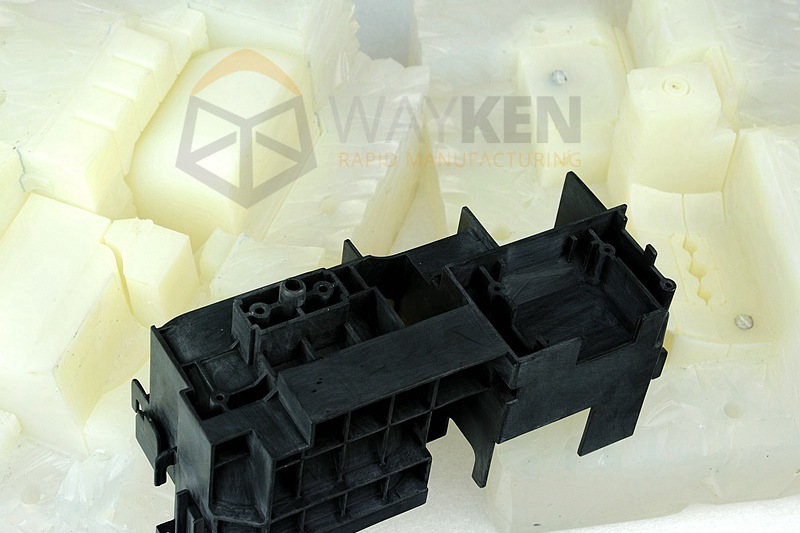
5. A Wide Variety of Resin Materials
Urethane casting supplies are wide in range and properties. The materials can be rigid, elastomeric, colored, clear, painted, and coated. Each option is perfect for its own condition. Some of the urethanes are similar to the more popular polymers (ABS, PMMA, PC, PP, PA), some have unique properties, for example, transparent flexible urethanes or heat-resistant ones (up to 120℃), there are even urethanes that can withstand open fire provided by the polyurethane casting services in China.
The combinations and uses of urethane materials are surely many and expansive.
6. Polyurethane Vacuum Casting Applications
Low Volume Manufacturing / Short Production Runs
The urethane vacuum plastic truly shines in low volume manufacturing. The capital investments in such cases are just not profitable, so manufacturers prefer to use less durable but easier to manufacture urethane molds.
Engineering Verification / Functional Testing
Urethane molds are cheap so if you are making a functional prototype and it has proven ineffective, you can just throw the mold away and make a new one while not losing much money. That’s why cast urethane molding parts are used as prototypes and pre-marketing batches.
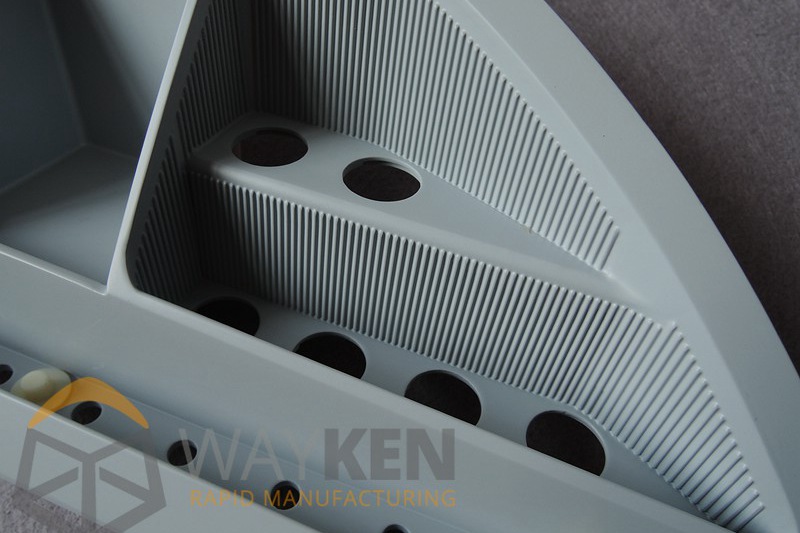
Aesthetic Models / Color & Texture Studies
One of the advantages of silicone molding is that it can show you what your end-product will look like without any capital investments. You can even make a number of parts with different colors using simple colorant and compare the results to choose the perfect version.
Marketing Ready / Display Models
Outstanding surface finish and detail make vacuum casting a good choice to create aesthetic mockups or visual prototypes for potential investors or exhibitions. And if some changes need to be made, you can just change the master pattern and create a new mold for a minimum cost.
About Author: Mandy, WayKen Project Manager
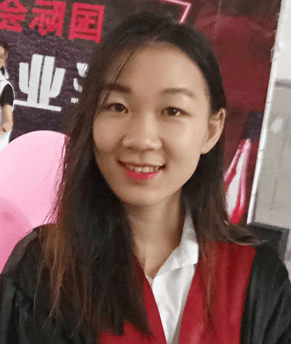
Mandy Meng is a self-motivated person, a professional sales engineer who loves to write something to share her passion with readers. Recently, other work you may be interested in urethane molding.