Dwindling profit margins in every business has almost forced everyone regardless of scale to adopt some sort of maintenance management into their workflow in order to save guard the company assets and prevent unnecessary losses. Now while traditionally maintenance management is handled by a human crew under a specialised manager, with the advent of new technology it has become increasingly apparent that maintenance is a sector where computers are much better suited that their human counterparts.
The major reason behind this is that while human maintenance is mostly reactionary, ie, the crew springs into action once a piece of hardware goes out of action, a CMMS solution is software based and can perform preventive maintenance. This means a CMMS solution can not only prevent most random outages from ever occurring, they can also end up saving the company a ton of money by conducting timely repairs and thus increasing the life span of any assets owned by the business.
However, for a CMMS to do this properly, it needs some human intervention as the software needs to be set up properly and have a skilled manager monitoring it from time to time in order to achieve optimal efficiency. It is these specific details that we will delve into in today’s piece so that you can use the power of preventive analysis in your CMMS systems and save a large chunk of money.
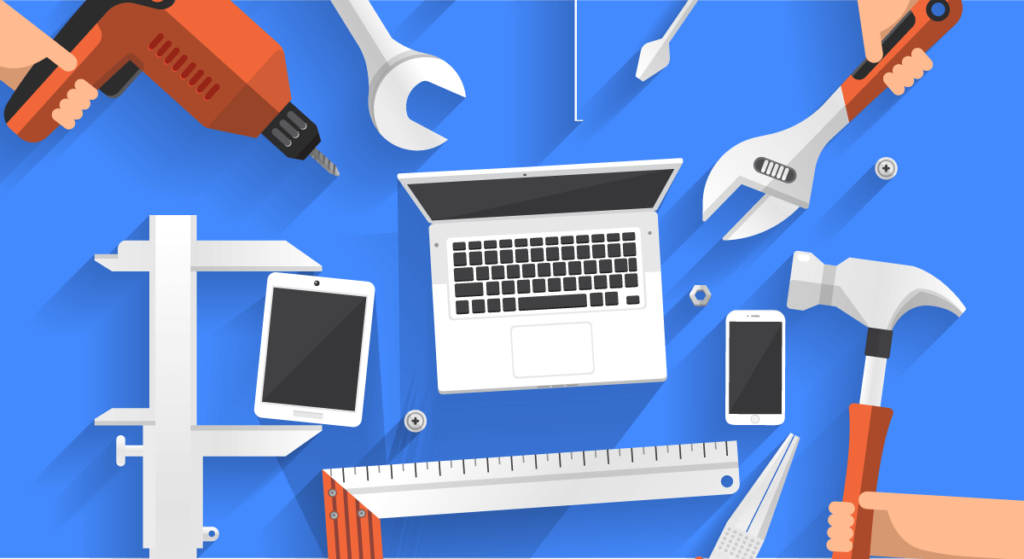
1. Making Sure Every Piece of Equipment Is Registered with the CMMS
Most predictive CMMS systems work on a very complex predictive model that takes into account multiple factors like number of assets involved, the human resource at hand and the current workload before it comes up with a maintenance schedule as well as the work order. Thus it is imperative that every asset of the company is registered onto the CMMS system so that the software can have an exact idea of the resource allocation activities that it needs to perform.
2. Following Through With Maintenance Schedules
Preventive Maintenance is only successful and worthwhile if the maintenance crew is proactive and takes heed of early warnings from the CMMS system and keeps all the equipment under a tight maintenance schedule as suggested by the CMMS software. In fact while creating an automated preventative maintenance schedule is one of the primary jobs of a CMMS, making sure that the actual maintenance work is performed falls under the purview of the manager who is looking over that sector.
3. Keeping an Eye On the Real Time Data
Most modern CMMS systems show real time data readings from various sensors placed on running hardware. While analysing this data is mostly something that the software itself is pretty adept at, sometimes a human eye can spot patterns in the data that might have been missed by the machine. These data patterns are crucial when it comes to identifying pain points in the manufacturing process as they represent a potential disruption in the workflow. A manager can use this bird eye view of the entire manufacturing process to make mission critical decisions that can end up saving a company thousands of dollars in potential revenue.
Broadly tuning in these factors can help get the most out of the preventive measures that are already prebuilt into your CMMS software and can in the long term make a pretty significant difference to the bottom line of any company.